KRAL Screw Pumps.
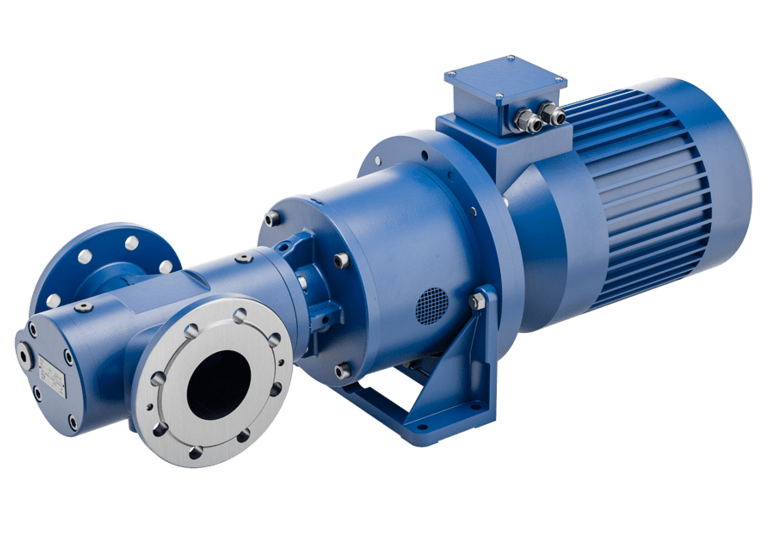
Delivery rate: 5 to 2,900 l/min.
Max. differential pressure: 16 bar.
Temperature range: -20 °C to 180 °C, magnetic coupling to 300 °C.
Housing: Nodular cast iron EN-GJS-400.
Screws: Steel, nitrided.
Approvals: ABS, BV, CCS, DNV, GL, LRS, MRS, NK, RINA.
ATEX: II 2 GD b/c group II,
category 2.
Heating: Electrical, media or steam.
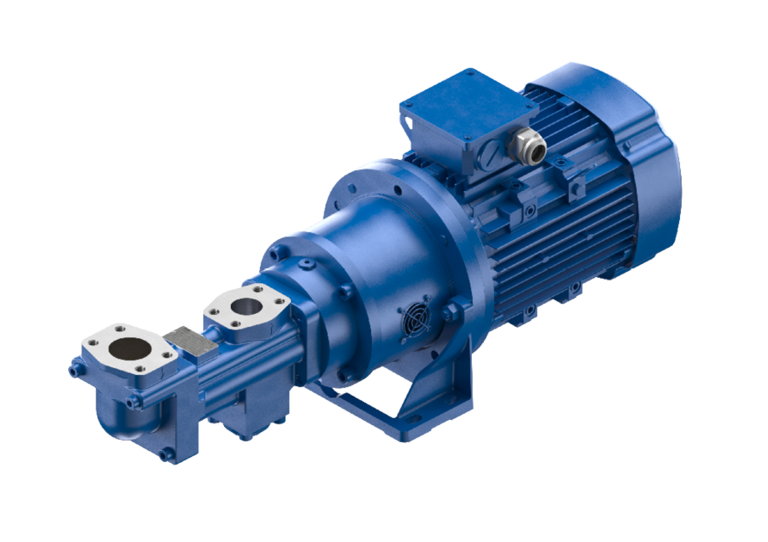
Delivery rate: 5 to 660 l/min.
Max. differential pressure: 25 bar.
Temperature range: -10 °C to 120 °C
Housing: Nodular cast iron EN-GJS-400, Steel.
Screws: Steel, nitrided.
Approvals: ABS, BV, CCS, DNV, LRS, MRS, NK, RINA, KR.
ATEX: II -/3 G Ex h IIC T4...T2 -/Gc X., with mechanical seal.
II -/2 G Ex h IIC T4 ... T2 -/Gb X., with magnetic coupling.
API: Construction according to API 676.
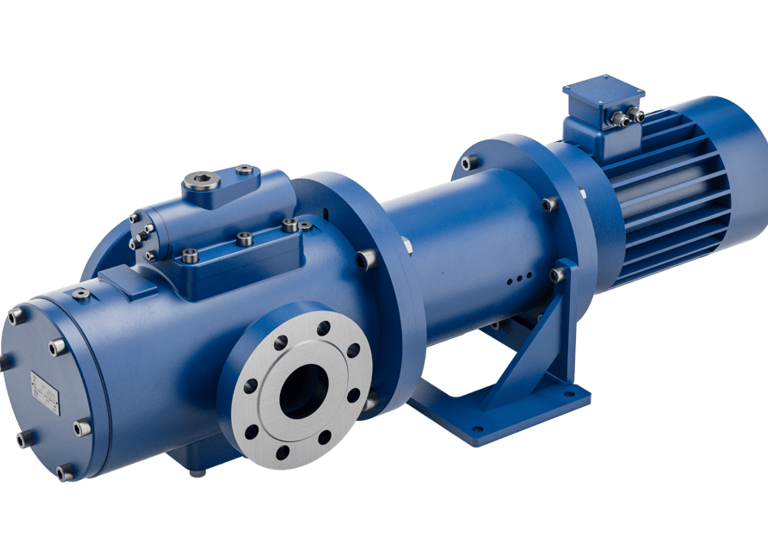
Delivery rate: CK: 5 to 1,750 l/min / CL & CG: 5 to 3,550 l/min.
Temperature range: -20 °C to 180 °C, magnetic coupling to 300 °C.
Pressure range: 70 bar; 100 bar.
Housing: Nodular cast iron, steel and aluminium.
Screws: Steel, nitrided.
Approvals: ABS, BV, CCS, DNV, GL, LRS, MRS, NK, RINA, KR.
ATEX: II 2 GD b/c group II,
category 2.
Heating: Electrical, media or steam.
API: Manufactured to conform
with API.
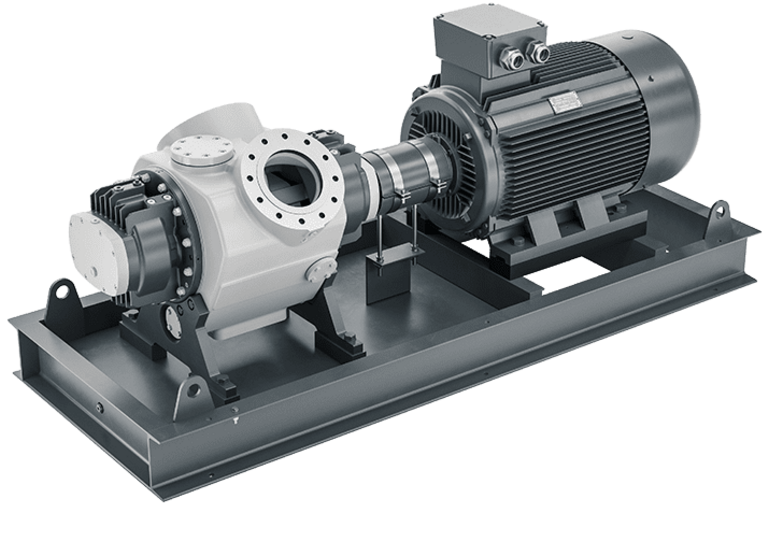
Delivery rate: 330 to 17,660 l/min or 20 to 1,060 m3/h.
Max. differential pressure: 25 bar.
Temperature range: -40 °C to +300 °C.
Housing: Ductile iron or welded steel.
Screws: Solid or engineered.
Approvals: ABS, BV, DNV/GL, LRS, RINA, others on request.
ATEX: II 2 GD b/c group II, category 2.
Heating: Electrical, media or steam.
API: Manufacturing according to API 676 possible.
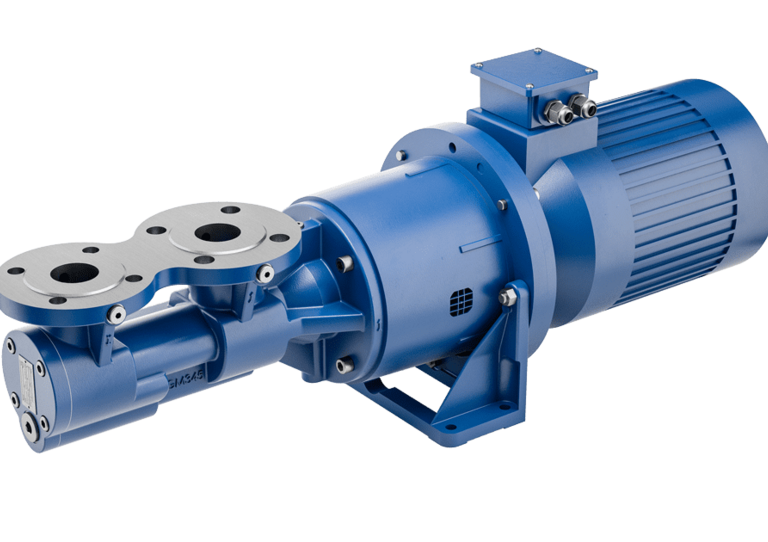
Delivery rate: 5 to 200 l/min.
Max. pressure: 63 bar.
Temperature range: -20 °C to 180 °C, magnetic coupling to 300 °C.
Housing: Nodular cast iron EN-GJS-400.
Screws: Steel, nitrided.
Approvals: ABS, BV, CCS, DNV, GL, LRS, MRS, NK, RINA, KR.
ATEX: II 2 GD b/c group II, category 2
Heating: Electrical, media or steam.
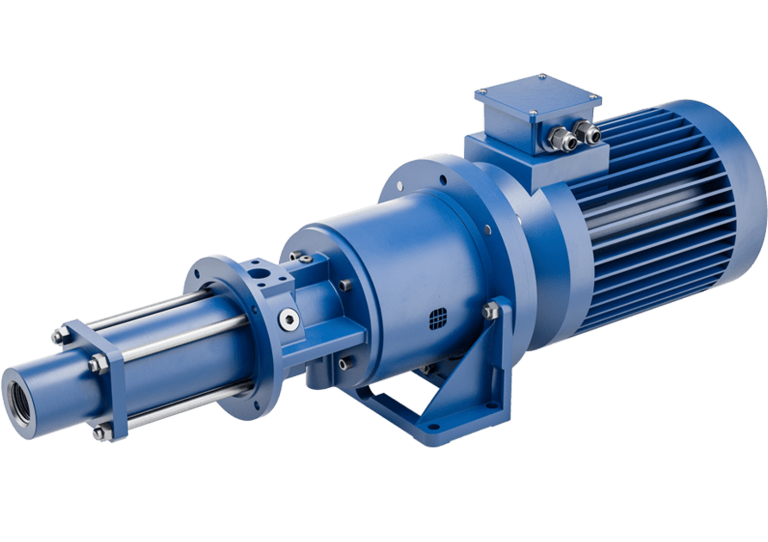
Delivery rate: 15 to 290 l/min.
Max. differential pressure: 120 bar.
Viscosity: > 1 mm2/sec.
Max. temperature: to 180 °C, magnetic coupling to 300 °C.
Installation: Wet or dry.
Spindle housing: Nodular cast iron EN-GJS-400, polymer-coated or other material options.
Screws: Steel, nitrided.
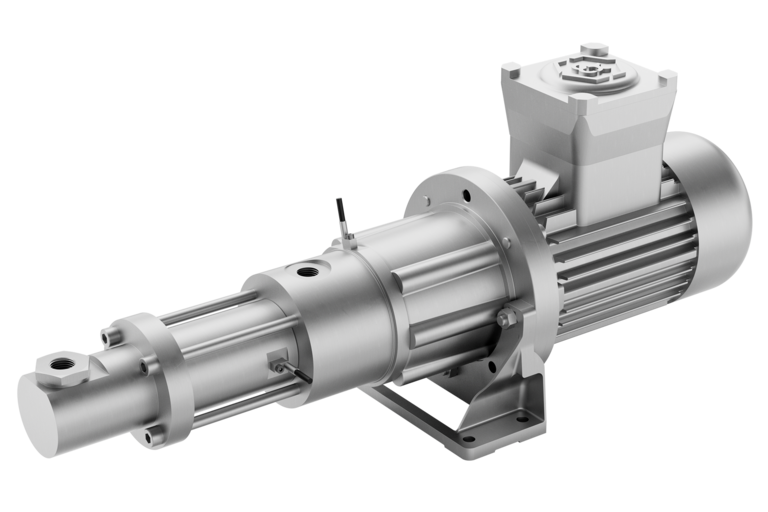
Delivery rate: 5 to 280 l/min.
Max. differential pressure: 120 bar.
Max. temperature: +80 °C.
Viscosity: 0.2 to 500 mm2/s.
Rotation speed: up to 4,000 min-1.
ATEX: Zone 1 & 2.
Future Fuels: Biofuels, Methanol, Ammonia, Ethanol, LFO, HVO, FAME.
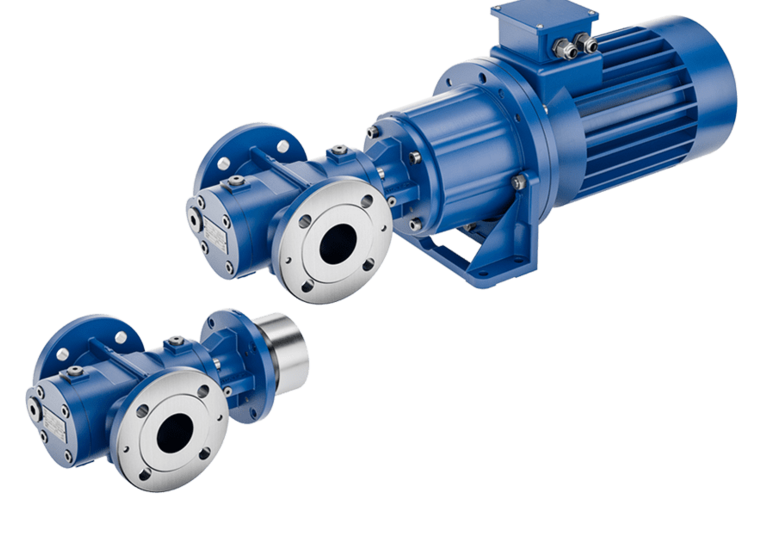
magnetic coupling.
Delivery rate: 5 to 3,500l/min.
Max. differential pressure: 100 bar.
Temperature range: -20 °C to 300 °C.
Housing: Nodular cast iron EN-GJS-400, steel and aluminium.
Screws: Steel, nitrided.
Approvals: ABS, BV, CCS, DNV, GL, LRS, MRS, NK, RINA.
ATEX: II 2 GD b/c group II, category 2.
Heating: Electrical, media or steam.
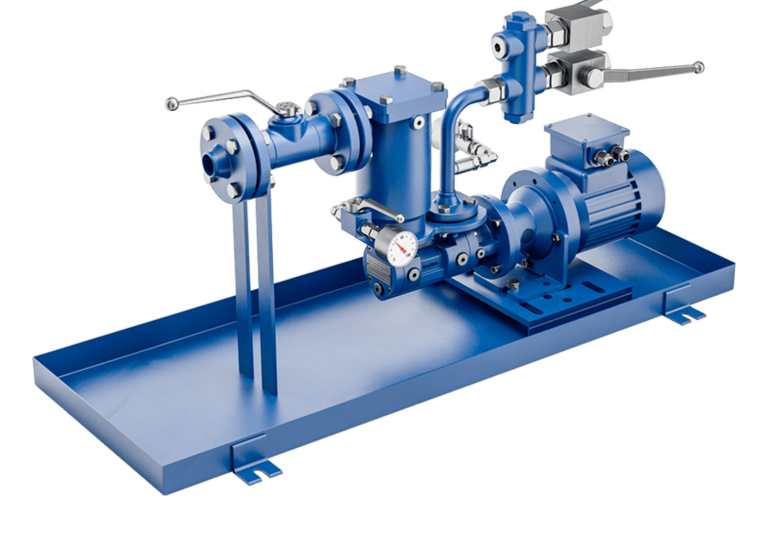
Delivery rate: 5 to 280 l/min.
Max. differential pressure: 40 bar.
Temperature range: -20 °C to 180 °C.
Housing: Nodular cast iron EN-GJS-400.
Screws: Steel, nitrided.
Approvals: ABS, BV, CCS, DNV, GL, LRS, MRS, NK, RINA.
ATEX: II 2 GD b/c group II, category 2.
Heating: Electrical, media or steam.
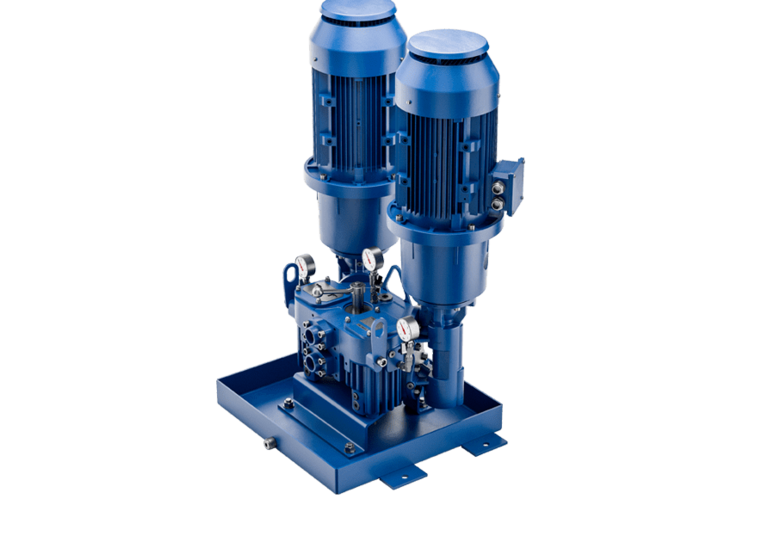
Delivery rate: 5 to 280 l/min.
Max. differential pressure: 40 bar.
Temperature range: -20 °C to 180 °C.
Housing: Nodular cast iron EN-GJS-400.
Screws: Steel, nitrided.
Approvals: ABS, BV, CCS, DNV, GL, LRS, MRS, NK, RINA.
ATEX: II 2 GD b/c group II, category 2.
Heating: Electrical, media or steam.
With KRAL screw pumps, you buy high quality and reduce costs for many years: through high flow rate, low-maintenance operation, flexible application possibilities, space-saving installation and long service life even with abrasive and corrosive media.
KRAL products offer maximum flexibility for variable operating conditions – 70 years of experience in the industry speak for themselves.
Good controllability of the positive displacement screw pumps.
KRAL screw pumps offer the advantage of a linear flow rate principle. This enables simple and cost-effective volume control via the motor speed, as well as a consistently high and continuous flow rate, even if the viscosities change.
This combination of cost-saving control with consistently high flow rates for high and low viscosity media is not possible with functional principles such as centrifugal pumps.
Low-pulsation pumping of liquids for various applications.
KRAL screw pumps are self-priming and pump fluids of different viscosities particularly gently and quietly. The pumped medium is not squeezed, there are no pressure pulses, which damage the pump, piping or other components or cause vibrations. Pumps, such as piston pumps, can damage the pump, the system and the pumped medium due to much stronger pressure pulsations. KRAL pump solutions are suitable for many different applications (e.g. oil, bitumen, polyurethanes) where operation without pulsation is necessary.
Screw pumps from KRAL offer high performance in a small space.
Space for setting up or installing of positive displacement screw pumps is expensive and often short. Compared to pump solutions with centrifugal pumps, for example, KRAL screw pumps offer a high flow rate, a small space requirement and high efficiency.
KRAL screw pumps are versatile and can be used in a wide variety of industries.
Pumping liquids is a demanding task. Whether lubricating oil or even if the medium is abrasive. When selecting and dimensioning a screw pump, the pumped fluids, the operating conditions, the installation site as the standards, guidelines and directives have to be taken into consideration. A great deal of application knowledge is required to ensure that no mistakes are made in the product or solution.
KRAL offers this comprehensive knowledge. The company has been manufacturing self-priming screw pumps since 1950 for many industries and uses its decades of application know-how as well as its highly qualified employees for the continuous further development and innovation of its products.
In many situations, KRAL screw pumps therefore offer clear advantages over competitor solutions. Please contact us. We will be pleased to advise you on the best technical and price solution for your purposes.
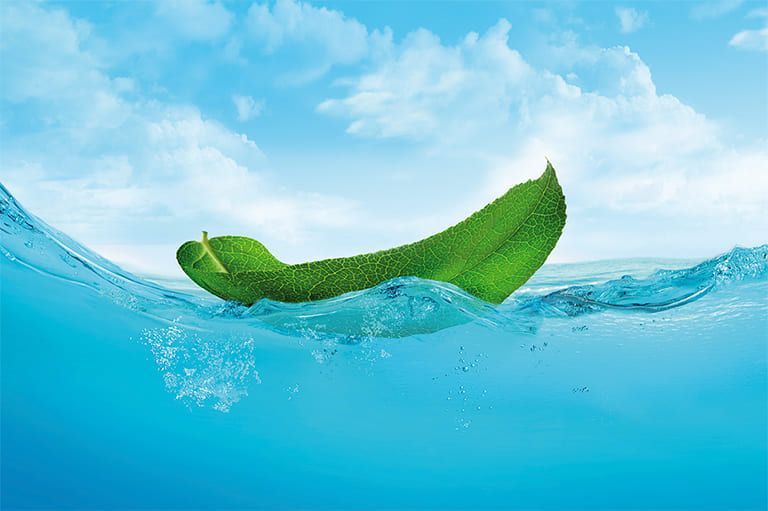
More and more vessels around the world will be equipped with KRAL pumps to meet the latest IMO regulations.
Why do so many companies rely on our pumps?
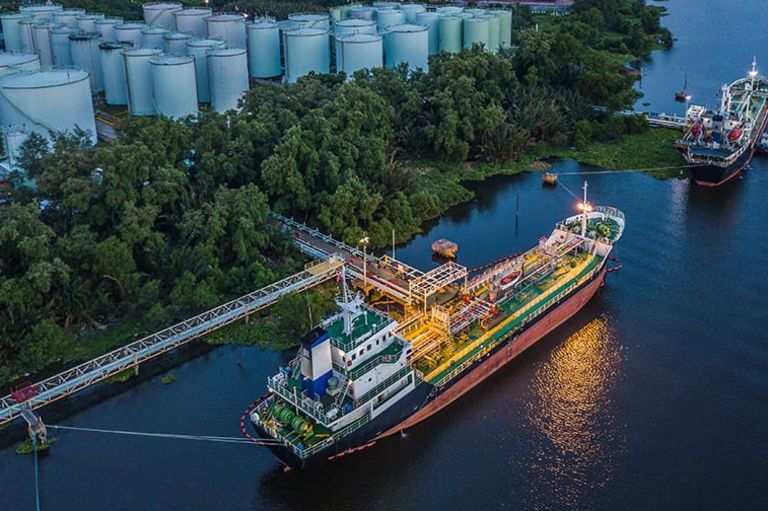
Why many, if one is enough?
KRAL pumps have a wide field of application in tank farms and terminals. All media, neutral, basic/acidic, aggressive, abrasive or gaseous, are safely sucked in, dosed and pumped.
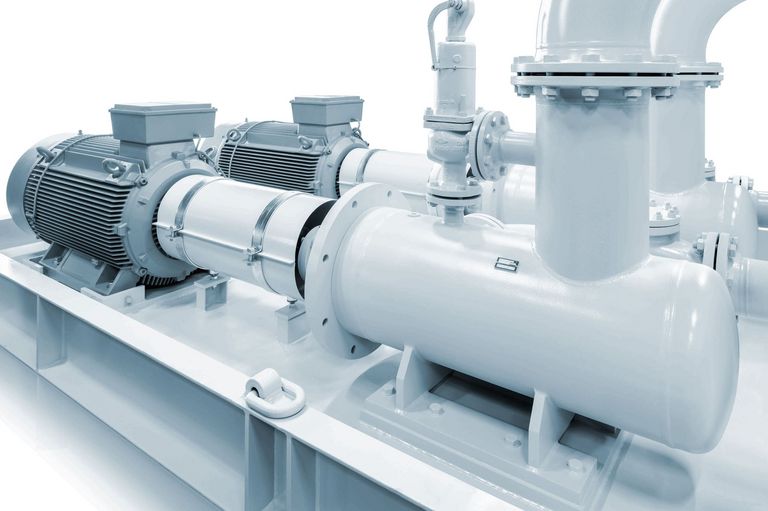
As pump specialists, we manufacture the core products of our pump modules ourselves. This knowledge clearly distinguishes KRAL from system manufacturers who only make the piping and do not consider the effect of the pumps on the system or the influences of the system on the pumps.
We develop continuously and produce every pump at our headquarters in Lustenau, Austria. This enables customer-oriented solutions and rapid reaction and delivery times. Take advantage of this. Contact us for an offer.
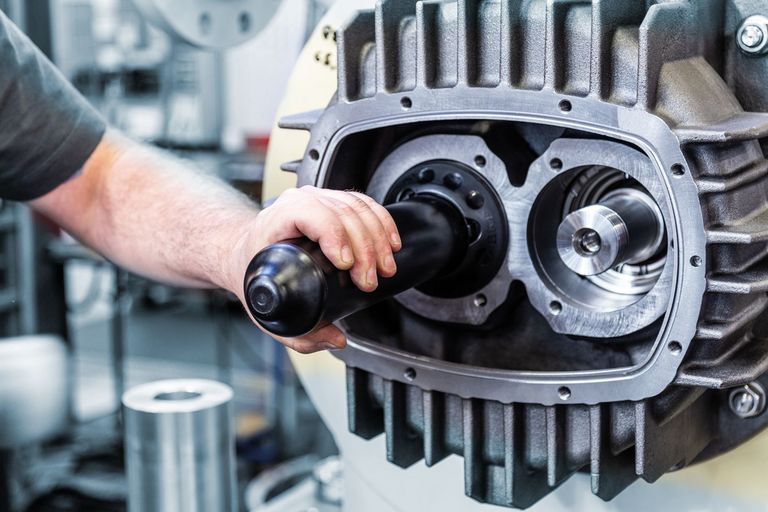
Through professional assembly, commissioning and maintenance of your KRAL products, you increase their service life, minimize costs and prevent failures. We can offer you attractive complete packages here. One of our employees will be happy to advise you.